Biodiesel in Mining: Your Questions Answered
From the Mine Safety and Health Administration’s (MSHA) limitations on diesel particulate matter and concerns over underground mining air quality, to the National Mining Association’s commitment to the Paris Climate Agreement and an increasing number of mining companies setting aggressive lower carbon targets — there are many reasons why reducing carbon intensity is becoming not just important, but also required.
All this has prompted many mining fleet managers to evaluate lower carbon fuel and power solutions for their diesel-powered equipment. While some solutions — such as hydrogen fuel cells and battery-powered electric — are in the early stages of viability, bio-based fuels such as biodiesel and renewable diesel are available today and can make an immediate impact without investment in any new infrastructure or equipment.
However, many fleet owners and managers still have questions about the transition to bio-based fuels. For answers, we turned to Rajani Modiyani (RM), Senior Manager, Emerging Markets at Chevron Renewable Energy Group.
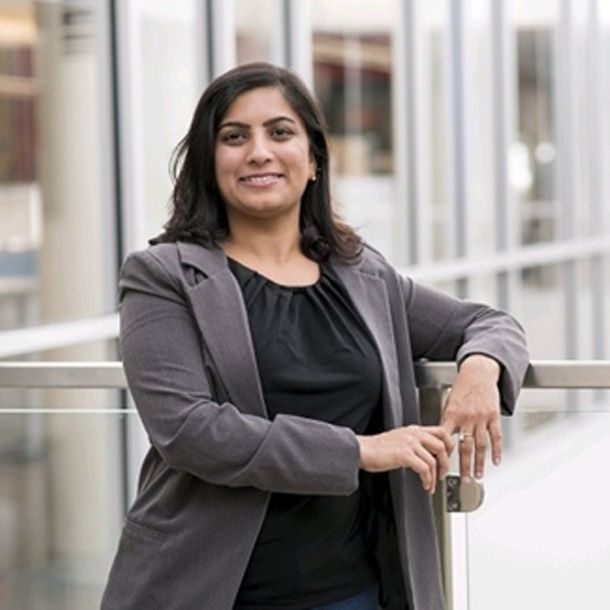
Rajani Modiyani, Senior Manager, Emerging Markets
Chevron Renewable Energy Group
Q: What is driving carbon reduction initiatives for mining fleet owners?
RM: Driven by pressures from non-governmental organizations and a desire to improve underground air quality, numerous global mining companies like Anglo American, Rio Tinto and several others have established midterm and long-term CO2 reduction targets for their Scope 1, Scope 2 and Scope 3 emissions. These targets are actively monitored, and the progress toward these targets is evaluated by effective governance mechanisms that have been put in place.
Furthermore, obtaining and maintaining the license to operate has become a key risk identified by the mining industry. How a mine performs and plans to perform in terms of its impact to the environment (air, water and land) is a critical consideration in the process to obtain and renew licenses to operate.
Additionally, there are several mining operations that have an opportunity to reduce their current and future operating expenses by incorporating lower carbon solutions. For instance, underground mining operations incur a substantial cost in ventilating the mines, and incorporating lower carbon solutions can enable them to reduce the amount of infrastructure needed and thereby reduce the associated energy costs.
Q: How common is the use of biodiesel and renewable diesel in the mining sector today?
RM: Biodiesel blended at high levels has been commonplace in the underground mining sector for nearly 20 years due to its ability to reduce diesel particulate matter.
Surface mining companies have also been accelerating their adoption of biodiesel and renewable diesel to enable them to achieve their 2030 carbon reduction targets. In addition, these targets are also influenced by national and state policies and further enabled by OEM approval to use biodiesel and renewable diesel in mining equipment.
Several global mining companies have undertaken and completed extensive testing with biofuels and adopted it for use in surface mining equipment, globally.
Furthermore, the vast majority of key equipment and engine manufacturers have already approved varying levels of biodiesel blends. In several cases, OEMs approve the use of 100% renewable diesel (RD100) and/or biodiesel (B100) in their engines.
Q: How much do renewable diesel and biodiesel reduce carbon emissions compared to other fuels?
RM: Compared to petroleum diesel, biodiesel and renewable diesel may reduce carbon emissions by up to 100% for fossil carbon.1 Biodiesel also reduces total hydrocarbon by 70% and renewable diesel up to 40%.2 The carbon intensity (CI) score of both biodiesel and renewable diesel have also been consistently lower than LNG and hydrogen.3 Compared to electric, biodiesel may be about 56% more effective at reducing carbon when taking the power grid into consideration.4
Connect With Mining Experts
Q: For remote mine sites, is access to biodiesel or renewable diesel a hurdle?
RM: Biodiesel and renewable diesel are one the most accessible lower carbon solutions available in the market today. The supply chains for these fuels are starting to mimic that of petroleum diesel, and we continue to see evolution. For example, Chevron Renewable Energy Group has 9 biorefineries throughout the United States and roughly 50 terminals to make biodiesel and renewable diesel more readily available. Furthermore, the delivery partners we work with are typically the same ones that deliver petroleum diesel, as are the supply points.
In geographic regions that are more mature in their adoption of renewable diesel — such as in California, where low carbon fuel standards have been adopted — pipeline conversions to move renewable diesel are being evaluated.
Q: What blend levels are common between biodiesel and diesel in mining equipment?
RM: It’s very common to see B20 biodiesel blends (20% biodiesel / 80% diesel) on a volumetric basis in Tier 4 engines that are equipped with aftertreatment systems. In older model engines without aftertreatment systems, it’s common to see the approvals for biodiesel blends to be much higher — often more than B50 levels.
Q: What are some of the storage and handling differences with biodiesel as compared to diesel in the mining industry?
RM: Biodiesel can be used in existing diesel tanks, generally without any modifications. And because mining operations consume a great deal of fuel, typically without long breaks in operation, the fuel turns over very quickly. So, there isn’t much difference at all between storage and handling of biodiesel versus petroleum diesel.
The one exception is in cold weather extremes. The cloud point of biodiesel is different from that of diesel. For distilled biodiesel, storing at least a few degrees above the fuel’s cloud point is important. For biodiesel blends up to B30, heated or insulated tanks aren’t typically needed.
Q: Does a transition to biodiesel require any modifications to storage or engines?
RM: One of the biggest advantages of biofuels as a carbon reduction solution is that they can be implemented today within existing equipment and infrastructure, with little to no impact to operations. In fact, biodiesel offers some engine performance benefits, including improved lubricity and combustion, which helps to reduce DPF clogging and regenerations when compared to petroleum diesel.
Q: What advice would you give to someone in the mining industry that may be skeptical of integrating biodiesel?
RM: When evaluating various lower carbon solutions, I believe we need to take a holistic approach and evaluate the four criteria, namely: technology readiness, operational impact, economic viability and fuel availability.
Biodiesel and renewable diesel check all the boxes — from their ability to use in existing equipment, to causing no negative impact to operations, being cost-friendly to implement and readily available.
Most of the other solutions being evaluated appear to have a long way to go in one or more of those areas in order to make widespread adoption viable.
Moreover, as bio-based fuels see wider adoption, lower carbon producers like Chevron Renewable Energy Group are investing to further increase availability of these renewable fuels to market. One such example is the expansion we’re undertaking to increase our Geismar biorefinery’s renewable diesel production from 90 million gallons to 340 million gallons per year starting in 2024. So, it’s right around the corner.
Another relevant aspect is the availability of feedstocks that go into making our fuels. Chevron Renewable Energy Group has a diversified strategy to source feedstocks reliably. Our feedstock flexibility ensures more predictable pricing, greater availability and lower carbon intensity.
The mining industry can gain further confidence from the rail transport industry in terms of its successful deployment of biodiesel and renewable diesel. Chevron Renewable Energy Group has worked with key players like Union Pacific (UP) and Canadian National Railways (CN) to deploy our lower carbon solutions today. Interestingly, the base technology and its providers are typically the same for the rail freight and mining markets, making the adoption of this solution in mining even easier.
Ready to get started?
Contact us to discuss how we can be your lower carbon partner.
Footnotes
1 Product is produced from renewable oils and fats. Methanol used to make biodiesel and hydrogen used to make renewable diesel and SAF are typically made from conventional natural gas but can be produced from renewable resources.
2 CARB Assessment of the Emissions from the Use of Biodiesel as a Motor Vehicle Fuel in California "Biodiesel Characterization and NOx Mitigation Study." Durbin (2011)
3 https://ww2.arb.ca.gov/resources/documents/low-carbon-fuel-standard-reporting-tool-quarterly-summaries
4 Carbon intensity for EVs based on eGRID 2020 figures and EV EER of 3.8 for transit buses per National Renewable Energy Laboratory